- Oil Mill Machinery
- Oil Refinery Machinery
- Oil Processing Plant
- Solvent Extraction Plant
- Animal Oil Processing Machine
- Feed Processing Machine
- Palm Oil Mill
- Industrial Drying Machine
- Grain Processing Machinery
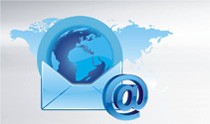
NEWS
What are the factors that affect oil dewaxing? What is the correct oil dewaxing?
Time:Tue-11-21 hits:
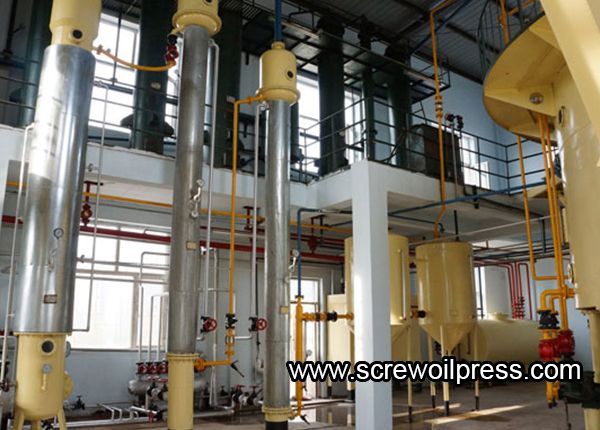
The main factors affecting dewaxing are temperature, cooling rate, crystallization time, stirring rate, auxiliary agents, conveying and separation methods, etc.
1. Temperature and cooling rate
Because the two hydroxyl carbon chains in the wax molecule are long, supercooling occurs during the crystallization process, and the lipophilicity of the wax hydroxyl group makes it supersaturated when it reaches the freezing point. In order to ensure the dewaxing effect, the dewaxing temperature must be fixed. It must be controlled below the freezing point of wax, but not too low, otherwise not only will the viscosity of the grease increase, which will cause difficulties in separating oil and wax, but also solid grease with a higher melting point will also be precipitated. The solid grease and wax will be separated from the oil together during separation Separate, increase the dewaxing loss of grease.
The crystallization temperature of the conventional method is 20-30°C, while the solvent method is controlled at 20°C.
Crystallization is a physical process and changes slowly. The whole crystallization process can be divided into three steps: melting waxy grease, supercooling, supersaturation, crystal nucleus formation and crystal growth.
Wax has a high melting point and can crystallize naturally at room temperature.
Naturally crystallized crystals are small and have different sizes. Some are peptized in oil, making it difficult to separate the oil and wax. Therefore, the oil temperature must be adjusted before crystallization to melt the wax crystals, and then the crystallization process is artificially controlled. In order to create good separation conditions-the crystal grains are large and strong.
The size of the crystal grain depends on two factors: the rate of nucleation (W) and the rate of crystal growth (Q). The dispersion of crystal grains is directly proportional to W/Q. During the crystallization process, W should be reduced and Q should be increased.
The cooling rate has a great relationship with W and Q. When the cooling rate is slow enough, the wax with a high melting point will crystallize first, and the heat of crystallization will be released at the same time.
The temperature continues to drop, and the wax with a lower melting point also crystallizes. The wax molecules that are about to be precipitated collide with the wax crystals that have crystallized, and they grow up with the precipitated wax crystals as the core, so that the crystal grains are large and few.
If the cooling rate is faster, the high melting point wax will precipitate, and it will have time to collide with the low melting point wax in the future, and the lower melting point wax will have been precipitated separately, making the crystal grains small and large, and entrained grease will inevitably be more.
In order to maintain a suitable cooling rate, the temperature difference between the coolant and the grease must not be too large, otherwise a large number of crystal nuclei will be formed on the cooling surface, which is not conducive to heat transfer, and is not conducive to the separation of oil and wax.
The cooling process should be carried out slowly, but it should not be too slow in terms of production. The appropriate cooling rate can be determined by cooling experiments.
2. Crystallization time
In order to obtain easy-to-separate wax crystals, cooling must be done slowly. And when the temperature gradually drops to the predetermined crystallization temperature, it is necessary to maintain the temperature for a certain period of time for crystallization (or aging, maturation). During the crystallization process, the crystal grains continue to grow, that is to say, it takes enough time from the formation of the crystal nucleus to the growth of the crystal into a large and strong crystal.
3. Stirring rate
Crystallization requires low temperature, but it is an exothermic process, so it must be cooled.
Stirring can not only cool the grease uniformly, but also collide the wax molecules that are about to crystallize, and promote more opportunities for crystal grains to grow uniformly. Stirring can reduce the formation of crystal clusters.
In addition to the growth of crystal nuclei during crystallization, several crystals may also gather into crystal clusters, which can entrain oil and increase the loss of grease during dewaxing. On the contrary, it can only rely on Brownian motion without stirring, and the crystallization rate is too slow, but the stirring cannot be too fast, otherwise the crystal grains will be broken (generally 10-13r/min).
4. Adjuvant
Different dewaxing methods require different auxiliary agents.
5. Solvent
Grease and wax have different structures and have different affinity for solvents, especially at low temperatures.
The presence of the solvent makes the wax easy to crystallize and helps the solid (wax crystal) and liquid (grease) phases to reach equilibrium faster, the resulting crystals are firm (less oil entrained), and the cooling rate can also be higher. At the same time, the solvent can reduce the viscosity of the system and improve the oil-wax separation effect.
6. Surfactant
The addition of surfactants helps wax crystallization.
The non-polar group in the surfactant molecule has a strong affinity with the hydroxyl group of the wax to form a copolymer. The surfactant has a strong polar group, so the polarity of the copolymer is much greater than that of the monomer wax, which makes oily -The surface tension of the wax interface is greatly increased, and the copolymer crystals are enlarged, the growth rate is fast, and it is easy to separate from the grease.
Phospholipids, monoglycerides, diglycerides, free fatty acids and soap produced in alkali refining in crude oil are all good surfactants, which can "pull" wax out of the oil under low temperature conditions. This is the main basis that rice bran oil can be dewaxed at the same time as low-temperature degumming and alkali refining.
However, there is still a certain affinity between wax and oil. The surface active substances in the above-mentioned oils do not have enough "pull force". To separate all the wax molecules in the oils, some powerful surfactants must be added. To achieve the desired dewaxing effect, polyacrylamides, aliphatic alkyl sulfates and glycolipids are commonly used.
7. Flocculant
Flocculant is a kind of electrolyte crystal promoter. Add a proper amount of electrolyte solution to wax-oil sol to increase the ion concentration in the sol, create favorable conditions for the negatively charged wax crystal grains to attract oppositely charged ions, and reduce the colloid.
The potential difference in the electric double layer structure reduces the repulsive force between the particles, and the stable system of the sol is destroyed, which causes the wax crystal particles to agglomerate.
The potential difference in the electric double layer structure reduces the repulsive force between the particles, and the stable system of the sol is destroyed, which causes the wax crystal particles to agglomerate.
8. Urea
Urea can selectively contain wax in the spiral tube formed by crystallization. The inclusion compound is easy to precipitate and separate from oil. Because of the different solubility of wax and urea in water, wax and urea are easy to separate.
9. Electrostatic dewaxing
It is a method of polarizing wax molecules by applying an uneven electric field, and the negatively charged wax crystal grains are enriched and settled at the anode under the action of the electric field to separate the oil from the wax.
10. Conveying and separating methods
When various delivery pumps deliver fluids, the turbulence caused by them varies in strength. The stronger the turbulence, the greater the shear force received by the fluid.
In order to prevent wax crystals from being broken by shearing force, when transporting grease containing wax crystals, a reciprocating plunger pump with weak turbulence and low shear force should be used, or compressed air, preferably vacuum filtration.
When the wax and oil are separated, the filtration pressure should be moderate, because the wax is compressible, too high pressure will cause the wax crystal filter cake to deform, block the filtration gap and affect the filtration rate, but too low pressure will cause the filtration rate to decrease. Production. The use of filter aids can increase the filtration rate.
11. Oil quality
The colloidal impurities in the grease will increase the viscosity of the grease, which not only affects the formation of wax crystals, reduces the firmness of the wax crystals, and makes it difficult to separate the oil and wax, but also reduces the quality of the wax (both oil and gum impurities are high) Therefore, the grease should be degummed before dewaxing. Wax has an adverse effect on alkali refining, decolorization and deodorization processes.
It is more reasonable to dewax the crude oil after degumming, and then to alkali refining, decolorization and deodorization.